EU PiG – 5S Lean Programme to improve work efficiency
A 5S lean programme was developed as an introduction to lean management to improve farm work efficiency. This led to a programme of continuous improvement underpinned by lean principles across the entire business of Patrick O'Keeffe's farm.
Ambassador: Patrick O'Keeffe, Ireland
Publication date: July 2020
Theme: Precision production
Challenges: Reducing costs
"I was most impressed with the 'buy-in' from my staff and the time saving as a result of the programme." Patrick O'Keeffe
5S lean programme results
Benefits
- Labour: 1 hour per day per person (€10,875 per year)
- No longer selling weaners due to poor return. Reduced slurry and labour costs (€10,980)
- Additional space: 348 finishers at 105 kg (€36,540)
- Dashboard system to document basic production data. Excel system on office computer to reduce labour (€6,500)
Costs
- Lean consultant – €1000 per day, approximately
- Plus, other improvements:
- Total cost savings – €30,755pa
- Total extra output – €36,540pa
Lean Programme to improve work efficiency
Lean management can be used to drive continous improvement, reducing costs and maximising efficiency. Improvements were achieved by mapping of areas, training of staff, implementing programme, monitoring progress and addressing ares for improvement.
Benefits
- Labour: 1 hour per day per person, equating to €10,875 per year
- No longer selling weaners due to poor return: Reduced slurry and labour costs, equating to €10,980 per year
- Additional space: 348 finishers at 105kg, equating to €36,540 per year
- Dashboard system documenting production data: Excel system on office computer to reduce labour, equating to €6,500 per year
- Plus other improvements
Total cost savings €30,755 per year.
Total extra output €36,540 per year.
The 5S lean programme in practice
As part of the 5S exercise, this was done by mapping areas, training staff, implementing programmes, monitoring progress (checklists and audits) and addressing areas for improvement. A control chart was used and was numbered and colour coded.
Once staff had engaged with the lean process, a value stream mapping exercise identified areas of ‘waste’ on the farm and engaged staff with improvement activities to reduce or remove that waste. This included reducing breeding group numbers to remove weaned piglets as a product, as the business was losing money. The increased space allowed increased stocking density in finished pigs without needing additional construction. Feed waste was reduced to just 2% of feed, and further improvements were made across the business, leading to an estimated reduction in labour and a saving in cost of production.
Back to: Precision production best practices
Case studies
More on the 5S lean programme best practice
5S checklist: Medicine storage
Let's Talk Pigs webinar: Becoming Lean – A Guide for Pig Farmers
Precision production best practice challenges
Dashboard systems/benchmarking
Increasing gilt and sow performance
Contact us
To access more information, contact RPIG (Ireland): Ciaran Carroll or EUPig@ahdb.org.uk
This project has received funding from the European Union`s Horizon 2020 research and innovation programme under grant agreement No 727933.
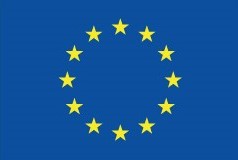