- Home
- Knowledge library
- Recover heat from the refrigeration system
Recover heat from the refrigeration system
How heat recovery works, the different types of heat recovery units and key installation points to consider.
Back to: How to ensure energy efficient water heating on dairy farms
Where water is to be heated and milk is to be cooled, there is obvious potential for saving energy and money by transferring the heat energy between the two systems. The heat normally thrown away by the refrigeration system can be captured to heat water and it helps the cooling system to work more efficiently too.
Heat recovery involves the transfer of ‘waste’ heat from the hot refrigerant gases in the milk cooling system to heat water. To make this happen, a Heat Recovery Unit (HRU) is either mounted in the water storage tank or in the pipe feeding water to the tank.
Water temperatures of up to 60°C can be achieved from heat recovery, saving 30% to 70% of water heating costs, depending on how much heat is available. Water temperature is ‘topped up’ using an immersion heater or conventional boiler system.
HRU key facts
There are two basic types of HRU; flow and storage. Regardless of type, an HRU is installed in the refrigerant line between the compressor and condensing unit where the refrigerant is at its highest temperature, typically 70–80°C. The refrigerant is placed in thermal contact with the water and heat transfer takes place.
The type of milk cooling system used will determine how best to install and operate the HRU to give optimum performance. Two important prerequisites are that:
- Operation of the HRU should not compromise the water heating systems ability to use night rate electricity, as this is the cheapest way to top up the temperature of the water
- The water heater should always be full of water at the appropriate temperature and at the required time, for example 85°C by the end of the morning milking for circulation cleaning
Figure 1. Installation of an HRU
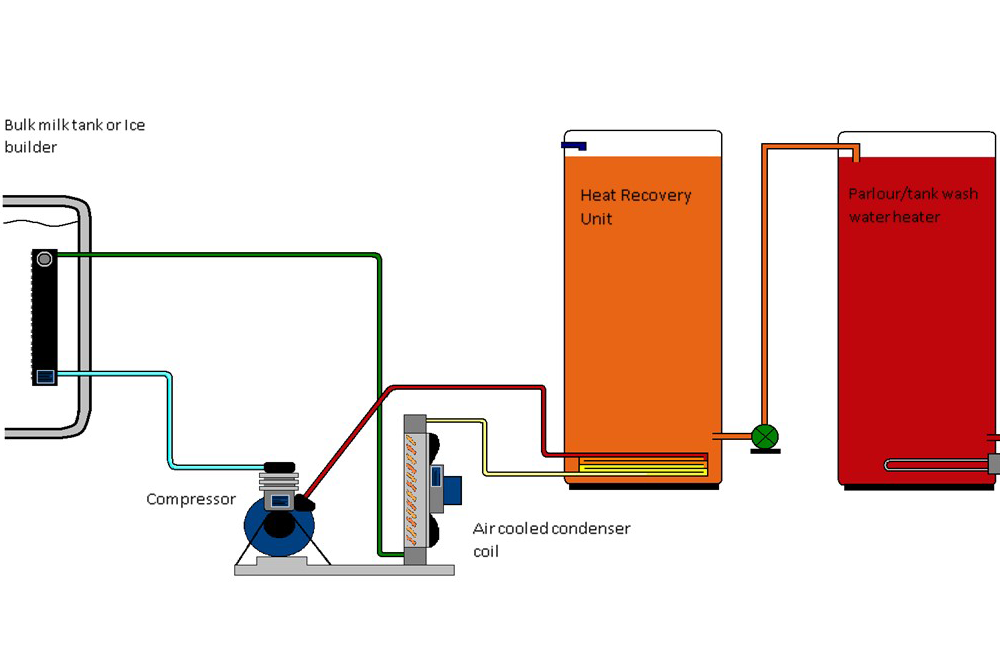
Flow based HRU
As the name suggests, this type of HRU relies on a flow of water passing through the heat exchanger at the same time as hot refrigeration gas flows in the other direction. Heat from the refrigerant gases passes across the plate surfaces to warm the water. The construction of these heat exchangers is similar to that of the milk-to-water plate exchangers often used to pre-cool milk.
The temperature of the water from this type of HRU can be as high as 60°C. This must be stored in a well-insulated tank to minimise heat loss prior to use.
The key to obtaining the best performance from this type of HRU is to ensure that water flow occurs whenever the refrigeration compressor is operating.
The system can therefore be controlled by:
- A direct link to compressor operation switching on the water flow when the compressor starts
- Fitting a time-switch to match normal compressor operating times
- Installation of a thermostat which switches on the water flow when an increase in refrigerant temperature is sensed
Two types of flow based HRU’s are available:
- Single pass – water is passed through the HRU once, at a very low flow rate and stored prior to use
- Circulation – water is circulated at a higher flow rate from a storage tank through the HRU and back again whenever the compressor is operating
On balance there is little performance difference between the two systems.
Storage based HRU
A storage based HRU is essentially an insulated water tank with a heat exchanger built in to it. The two most common designs pass the hot refrigeration gas through either:
- A coil of copper pipe within the tank
- A voided plate attached to the outer surface of the tank
With this type of heat recovery system heat transfer will always take place when the compressor is running, as long as the stored water is colder than the refrigerant.
The HRU effectively becomes a hot water header tank connected to the conventional water heater. This is a simple system which will operate independently to the volume and time that hot water is drawn from the tank, so no special control system is necessary. The water holding capacity of this type of HRU should be about the same as the water heater.
What to consider when installing an HRU
An HRU interacts very closely with the refrigeration system and it is advisable to take steps to ensure that both operate satisfactorily together:
- Anti-vibration fittings should be fitted to reduce the transmission of noise and vibration which can cause failure of the refrigerant pipes and fittings
- It is possible to over-cool the refrigerant, and so reduce the cooling capacity of the bulk tank
- It is possible sometimes for liquid refrigerant to flow back from the HRU into the compressor outlet. A non-return valve should be fitted to prevent this
In many cases none of these are a problem but it emphasises the need to use an experienced refrigeration engineer who can advise you accordingly. Water connections between the HRU and water heater should be insulated, as temperatures of over 60°C can be achieved.
Savings from installing an HRU
The figures in Table 1 are based on the results from tests on 40 farms over a 12 month period, and adjusted to reflect the requirements of a 100 cow herd size.
Table 1. Based on 11.5 p/kWh night rate, 16 p/kWh day rate
Electricity Saving kWh per annum | Cost Saving £ per annum displacing ‘night rate' electricity | Cost Saving based on displacing 'day rate' electricity | |
---|---|---|---|
Flow based HRU, single pass, IB tank |
2,330 |
£268 |
£373 |
Flow based HRU, circulation, DX tank |
1,464 |
£169 |
£235 |
Storage based HRU, IB tank |
3,041 |
£350 |
£487 |
Storage based HRU, DX tank |
2,329 |
£268 |
£373 |