- Home
- SmartPork | Cutting through the waste
SmartPork | Cutting through the waste
Launching a new business-focused campaign, SmartPork, designed to implement Lean practices by encouraging business improvements and increasing cost savings.
The single universal truth is that tomorrow brings something new. In agriculture that can be a blessing and a curse, at the very least it produces volatility, creating new challenges and opportunities with labour, technology, production goals and market prices.
Pork production is a complex series of processes with an ever-changing animal at its heart – the pig. As an industry, the pork sector has made significant strides in the costs of production, the standards of welfare and quality of product, however this is still a margins game.
What is SmartPork?
To remain competitive in this forever changing market, AHDB are launching “SmartPork” to inspire and enable UK pig producers to increase production efficiency. As part of this campaign, AHDB and Lean management consultants will be supporting 10 to 12 SmartPork Monitor Farms, as they continue to seek marginal gains amongst the complex processes of production.
Each farm will undertake practical programmes of process control/Lean improvement across gilt management and/or weaner management, with goals of increasing retention and weaning weights, with proven returns on investment. The recruited farms will share their Lean journey to the wider pork industry and showcase how implementing smart tools can improve overall business performance and productivity.
Importantly, as an industry we should not shy away from borrowing a good idea when we see one, after all, we are not the only sector that is a margins industry. Manufacturing has for decades been driven by market prices, just as we are. From those pressures they have devised systems of working that streamline each of their processes.
This process control allows consistency and reduction of waste that lowers the cost of production, not through cutting standards or jobs but by making processes more efficient. There are several names given to these management systems – Lean, 6 Sigma and Just in Time (JIT).
Lean specialists supporting the pork industry
Fedden USP is a highly successful and Lean-focused consultancy set-up in 2007, specialising in Lean, 6 Sigma and Continuous Improvement. They have delivered training and consultancy in Siemens, Ford, Bosch, Roll Royce Cars, Halma Group, and central government, to name but a few. This is in parallel with working with over 200 horticulture and agriculture companies from ornamentals, protected crops, field veg, dairy, and beef and pork producers.
Neil Fedden, Managing Director, said: “This combination of working with high-value engineering all the way through to small family-owned farms has allowed us to advise on what the latest thinking is for improving performance in operational environments.”
In recent years, Fedden USP has worked closely with AHDB, initially helping to develop the SmartHort programme which has delivered over £400K per annum of productivity savings in its first year. The emphasis of this programme was in not only going through the theory of Lean and productivity improvement but also how to apply it within your own business.
The course participants are encouraged to undertake a small business improvement project in line with learning the theory of how to conduct a waste walk, process mapping, problem-solving techniques, 5S/workplace organisation, visual management, and continuous improvement cycles using Plan Do Check Act (PDCA).
This is the basis of the SmartPork project, aiming to achieve similar positive productivity improvements. In addition to a combination of group and online training and 1-1 monthly support of projects, the participating business will also have a Value Stream Map produced for them. This looks at the whole business in terms of the main value streams, costs and key performance metrics and identifies where improvement activity will have the biggest benefit. This will then be the focus of improvement activity that the course participants will look at when they start applying the Lean theory.
Debbie Fitzgibbon, David Crowfoot and Neil Fedden from Fedden USP will work with pig producers. Between the team, there’s over 90 years’ experience of Lean and business improvement gained in the Japanese, US and UK automotive industry.
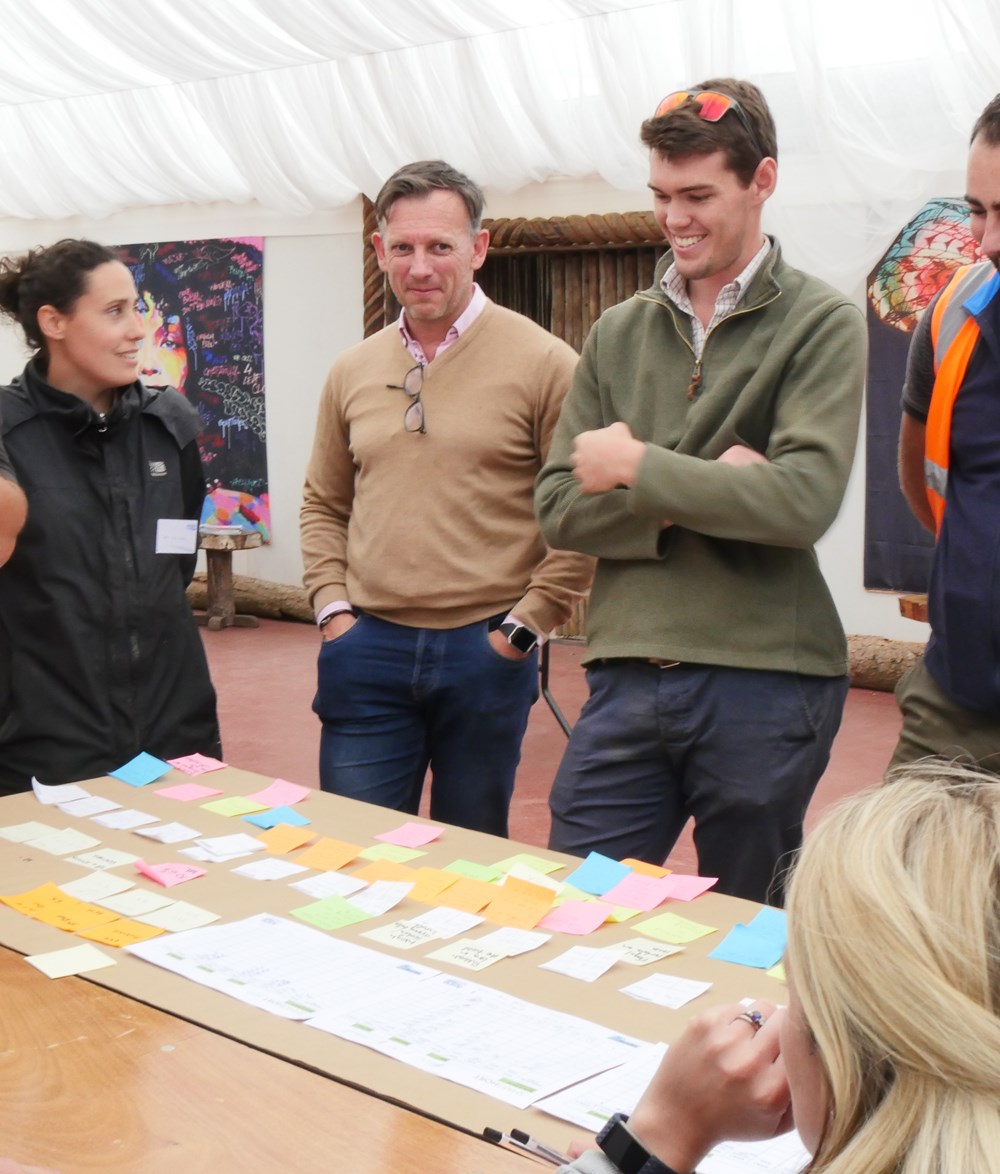
Become the master of Lean
Quality should be at the heart of everything we do, ensuring the industry delivers a high-quality product to our consumer and that producers maintain the high-quality from production to distribution.
SmartPork gives farmers an opportunity to take part in a nationally recognised qualification in Lean Manufacturing Operative in standards. The course will support their career development and at the end of it they will have the opportunity to gain a level 3 qualification. The fact that SmartPork provides staff with a recognised Lean qualification means that it’s also a tool for staff engagement and motivation.
Lean can be applied to all aspects of a business aiming to cut costs by introducing tools that can change their way of thinking and response to market needs. It can help producers to remove or minimise activities that don’t add value to the production process, such as holding of stock, repairing faulty products and unnecessary movement of people and products around the business. The workshops will help disseminate the learning behind Lean and teach producers how to:
- Improve overall business productivity
- Improve business efficiency and quality
- Make the most of resources and staff
- Avoid waste and improve financial status
Lean in action: Case study
Whatever the system for process control, the benefits are evident. A leading producer with experience in Lean processes told us: “You solve one problem hoping that after, you will travel into calmer waters. That never happens, once you solve a problem more will appear on the horizon.
We all run a production business that is a process. That process is producing not just any old pigs, but pigs with as uniform a weight as you can and a population that is as healthy as we can make them for as little money as possible. All this “process” requires control, if you do not control it, it will control you. Set production parameters that you can measure, meet and evaluate. Once you have done that stick to them. Over time, these individual parameters can be re-visited, and measurable changes made one at a time.”
The use of Lean techniques allowing a business to be agile may seem like an oxymoron but the graph from the same producer below shows that is not the case.
- The grey line shows the variance and volatility in their farrowing rate before introducing Lean techniques, such as standard operating procedures.
- The blue (dotted) line shows the farrowing rate after introducing Lean techniques.
- More powerful still is the red line, this is the farrowing rate whilst dealing with an outbreak of PRRS. Despite some increased variability, the use of Lean allowed the business to be agile enough to react and deal with the increased pressure, ultimately maintaining business performance.
How to make your business Lean?
The pork industry is facing constant change, so why not take the chance to improve, understand and implement powerful Lean tools.
The SmartPork hub will bring together AHDBs resources and offerings in people and process management, innovation and hardware, as well as supporting new technologies such as data capture. This offers producers the chance to track business performance, targeting labour and resources (which are always in short supply) at the processes, making the biggest impact.
Keep an eye out for any SmartPork activity across AHDB digital platforms and our upcoming in-person closed Lean Workshops and Pig Club events. There are many ways to get involved; join our AgriLeader forum, access our Lean tools or become AHDB’s Lean Champion.
Find out more information by visiting, ahdb.org.uk/smartpork.