- Home
- Gilt Watch® Early Successes
Gilt Watch® Early Successes
Explore a Gilt Watch® case study that successfully undertook methods to standardise farrowing groups.
Gilt Watch® mentors have shown that controlling some of the processes around gilt selection, farrowing groups and nutrition by parity, substantial reductions in variation and performance can be achieved.
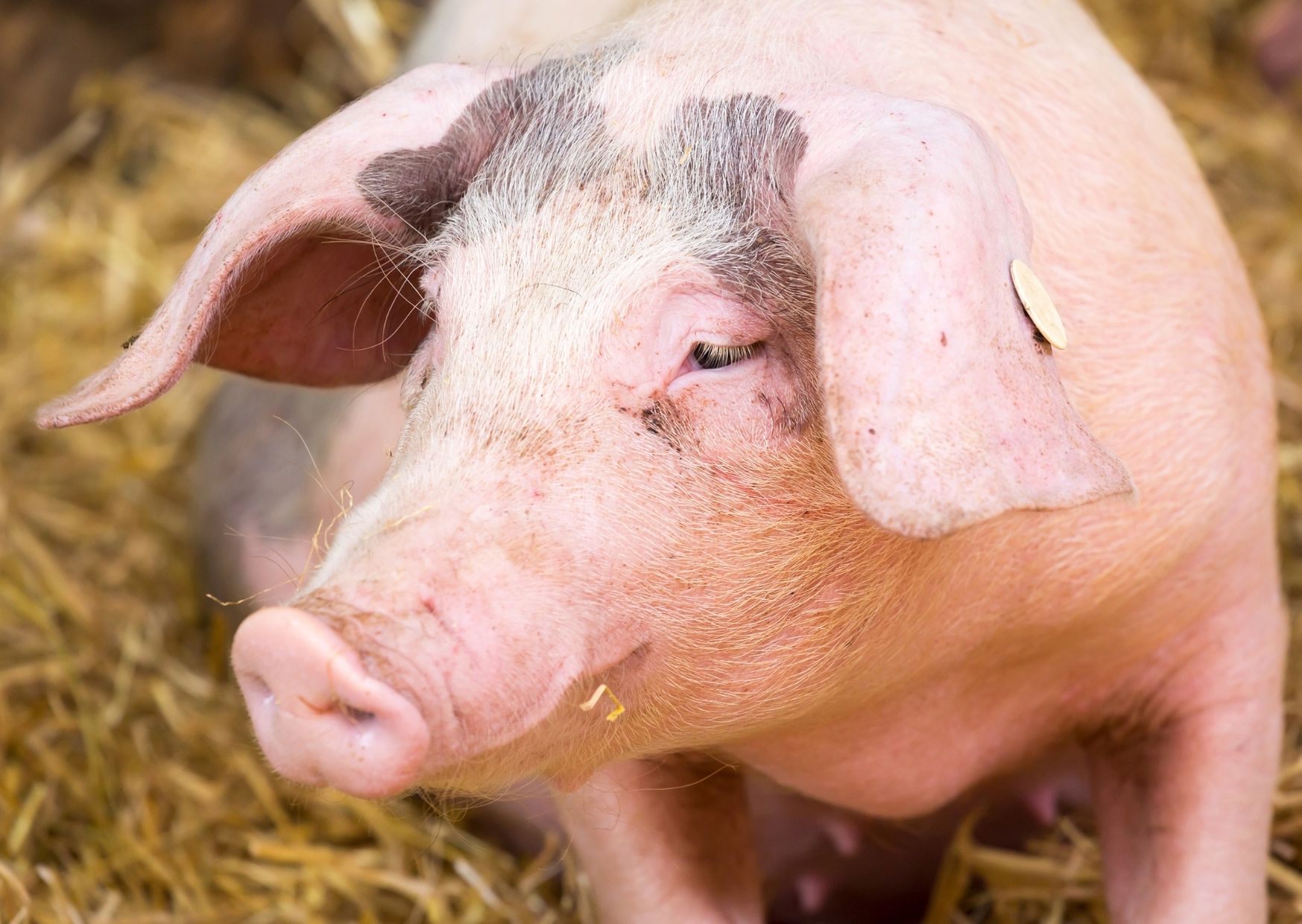
Reducing variation
Prior to 2010, one of the Gilt Watch® members had substantial variation in their key performance indicators (KPIs) such as farrowing rate. They undertook a process of standardising their farrowing groups in terms of numbers of services and parity profiles.
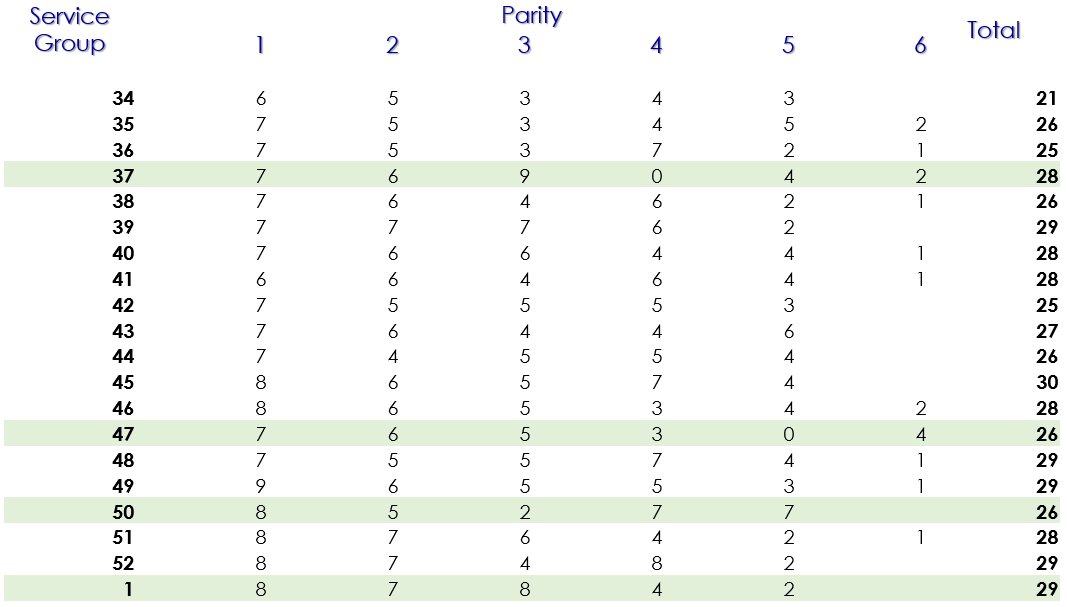
The parity profiles demonstrate a strict adherence to a 5-parity structure, with parity 6 animals only being used when absolutely essential and in minimal numbers. It should be noted there is an allowance for some variation as this is a biological system subject to variation and external forces (weather, disease and market pressures). The impact over a less coordinated and standardised approach is clear from the performance recorded over time.
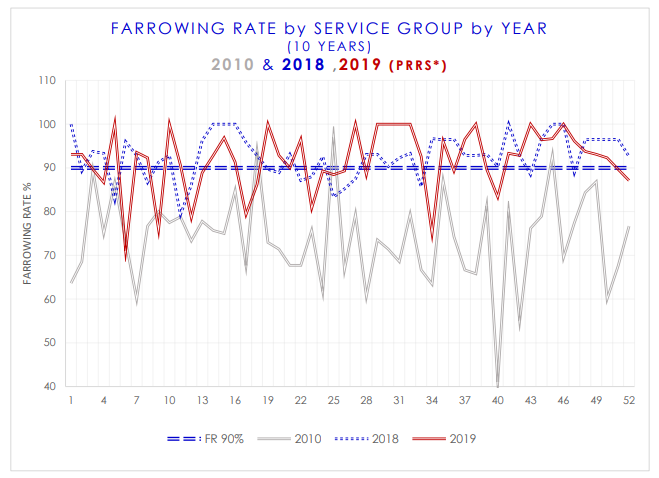
The graph shows clearly the impact that standardisation of the parity profiles has had on this business. The grey line is the performance prior to standardisation and shows substantial variation, and performance that falls short of the 90% farrowing rate KPI. Post-standardisation of processes (blue dotted line) shows it is clear that variation, while not eliminated, is substantially reduced, and performance against the KPI is increased.
Even more telling is how a standardised system reacts to external pressure. The red line on the graph shows the impact of a PRRS outbreak on the unit. While there is increased variation in performance, importantly it is not as severe as prior to process control, there is increased resilience. You can also see that, despite the variation, overall performance against the KPI is still strong.
In summary, embedding standardised processes with clear metrics to measure performance can make a substantial impact on overall business efficiency.
Read Simon Watchorn's full case study to understand his Lean journey and findings.